OUR PROCESS
The Process
All our process is hands-on, showcasing the artistry and dedication of our community. We source cotton from local farmers, which is then spun by local women’s cooperatives. Young staff members handle the dyeing process, while local women take care of winding the threads. Our master artisans skillfully weave the fabric, and dedicated women complete the fringe work and other finishing touches. Every aspect of our production is manual and labor-intensive, emphasizing our commitment to craftsmanship.
About us
BY FIREW KONJO
Welcome to Shimena, a social enterprise dedicated to preserving the ancient art of weaving while empowering artisans in southern Ethiopia. Founded and managed by Firew Konjo, a skilled weaver artisan, Shimena takes its name from the Amharic word for ‘weaving’, symbolizing our commitment to this timeless craft.
Established in 2014, Shimena offers a diverse range of products, including scarves, hats, ponchos, home decor items, and towels. Our operations involve over 100 artisans working across two workshops in Arba Minch, where we handle the entire production process—from spinning and dyeing to weaving, stitching, finishing, and quality control. Each month, we proudly produce around 2,000 unique pieces.

Our journey began with the USAID-funded Ethiopian Sustainable Tourism Alliance (ESTA), which focused on community-based tourism and craft development. Although the program concluded in 2013, many artisans faced challenges in accessing markets due to marketing skills and language barriers. In response, Firew Konjo transformed the NGO model into a sustainable business, enabling artisans to sell their crafts in local, Addis Ababa, and international markets.
At Shimena, we are not just creating beautiful woven products; we are also committed to uplifting women and providing them with livelihood opportunities. By promoting weaving as a respected and profitable profession, we aim to change perceptions among the youth and support environmental sustainability, all while ensuring better income for the communities we serve. Join us in celebrating the rich heritage of weaving and the artisans behind it.
Learn
Firew learnt how to weave at a very young age, from his uncle who was a master weaver.
Market
Over the years, weaving started to decline and artisans began shifting to other professions due to the craft losing its value
Creative
Firew's passion towards weaving & a strong desire to restore its value, while supporting his community, led to the establishment of Shimena
Supportive
Traditionally, weaving was a man's job. But Firew, through Shimena, is now able to train women to weave!

Our Process
Cotton Farm
Our raw cotton is sourced from farms just 10 km from our workshop in Arba Minch.
Spinning
Our textiles are crafted using handspun cotton from the skilled women of the Gamo Mountains.
Dyeing
At Shimena, we are committed to using natural and eco-friendly Reactive dyes in our Arba Minch workshop.
Weaving
Weaving has been a vital tradition in Ethiopia for centuries, particularly in the Gamo community, where each compound has its own permanent loom.
Finishing
In Arba Minch, we employ a dedicated team of young women from the local community, many of whom gather firewood from the nearby forests
Our Story
Firew Konjo
In the highland of Gamo, located in southwestern Ethiopia, Firew konjo grew up watching his uncle, who was one of the community’s master weavers, weave intricate textiles .The Gamo people were known for their exceptional weaving skills, and it was a tradition passed down from generation to generation. As Firew grew up, he became fascinated with the art of weaving and the cultural significance it held. Years later, Firew started shimena, a brand dedicated to preserving the traditional of sustainable, handmade production using raw cotton from local farmers and natural dyes from plants, grass, and roots in the local area. In addition to this, Firew promotes female empowering through his brand by employing and training women to practice weaving. Traditionally, weaving has been a male –dominated practice in the Region. By sharing his story, Firew motivates others in the community to engage weaving and uplifting the empowerment of women and the preservation of traditions.
Explore the tale of dedication, creativity, and a vision to spread the joy of nature’s beauty through the art of floral design. Discover the moments that shaped our founder’s path and paved the way for Florist to become a symbol of floral excellence.


Step 01
Cotton Farm
Our raw cotton is sourced from farms just 10 km from our workshop in Arba Minch. Once harvested, it is distributed to women in the nearby mountain communities, where they skillfully spin it into threads. This close-knit process ensures that each piece of cotton is deeply connected to the local environment, supporting the community while laying the foundation for our handcrafted textiles.
Spinning
Our textiles are crafted using handspun cotton from the skilled women of the Gamo Mountains. Spinning with a traditional drop spindle is a skill passed down through generations, and it’s almost second nature to these women. We embrace the unique, soft, and uneven texture of their handspun cotton, which adds authenticity and character to each piece, connecting our products to both heritage and craftsmanship.

Step 2
Let's Bring organic quality
Shimena Handcraft creates exceptional textiles using only organic materials, ensuring quality and sustainability in every handcrafted piece.

Step 3
Dyeing
At Shimena, we are committed to using natural and eco-friendly Reactive dyes in our Arba Minch workshop. Surrounded by the rich biodiversity of southern Ethiopia, we have access to a variety of local plant species, which we use to create vibrant, sustainable colors for our textiles. Each fiber is carefully hand-dyed in small pots, ensuring a unique, organic quality to every piece we produce.
Weaving
Our textiles are crafted using handspun cotton from the skilled women of the Gamo Mountains. Spinning with a traditional drop spindle is a skill passed down through generations, and it’s almost second nature to these women. We embrace the unique, soft, and uneven texture of their handspun cotton, which adds authenticity and character to each piece, connecting our products to both heritage and craftsmanship.
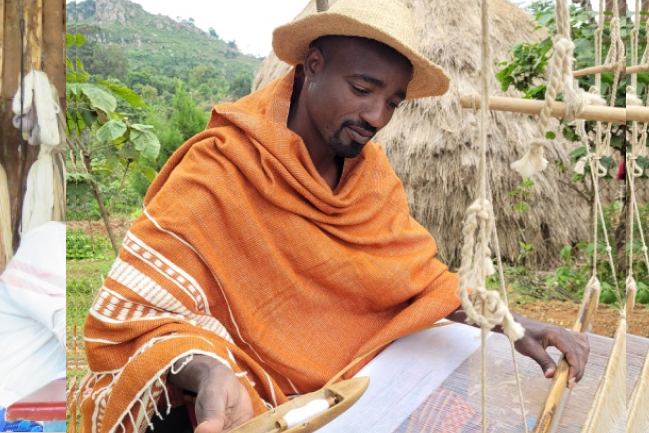
Step 4

Step 5
Finishing
In Arba Minch, we employ a dedicated team of young women from the local community, many of whom gather firewood from the nearby forests. They are responsible for the finishing touches on each product—trimming fringes, sewing labels, cutting edges, stitching cushions, ironing, and performing quality checks—ensuring every piece meets our high standards before export